Introduction
Ceramic manufacturing is an ancient craft that has evolved into a major global industry, with products that range from traditional pottery to high-tech ceramics. Renowned for its durability and versatility, ceramic is widely used across various sectors, including household goods, architecture, healthcare, and industrial applications. In households, ceramic products, such as dishes, tiles, and decorative items, bring both functionality and beauty. In healthcare, ceramics play a crucial role in creating biocompatible materials for implants and prosthetics, while in the industrial field, they are essential in making heat-resistant components. This industry not only contributes significantly to the global economy by generating jobs and advancing technological development but also holds deep cultural value. Ceramic arts and crafts reflect the unique traditions and creativity of different cultures, making ceramics a bridge between past and present, as well as a cornerstone in economic and cultural growth worldwide.
History of Ceramic Manufacturing Development
The origins of ceramics date back thousands of years, with early examples found in ancient civilizations such as China, Greece, Egypt, and Japan. Each of these cultures made unique contributions to ceramic techniques, with China renowned for its delicate porcelain, Greece for its decorated pottery, Egypt for symbolic clay artifacts, and Japan for its traditional raku and intricate pottery styles. Key historical milestones include the Chinese invention of porcelain during the Tang Dynasty (618–907 AD), which set new standards for ceramic quality, and the spread of glazing techniques across the Middle East and Europe during the medieval period, greatly enhancing durability and aesthetics. In modern times, technological advancements have transformed ceramics with innovations such as high-temperature kilns, mechanized production, and the development of specialized ceramics for medical and industrial uses. These inventions and adaptations have not only expanded the applications of ceramics but also established it as both an art form and a crucial industrial material, sustaining its evolution and relevance across centuries.
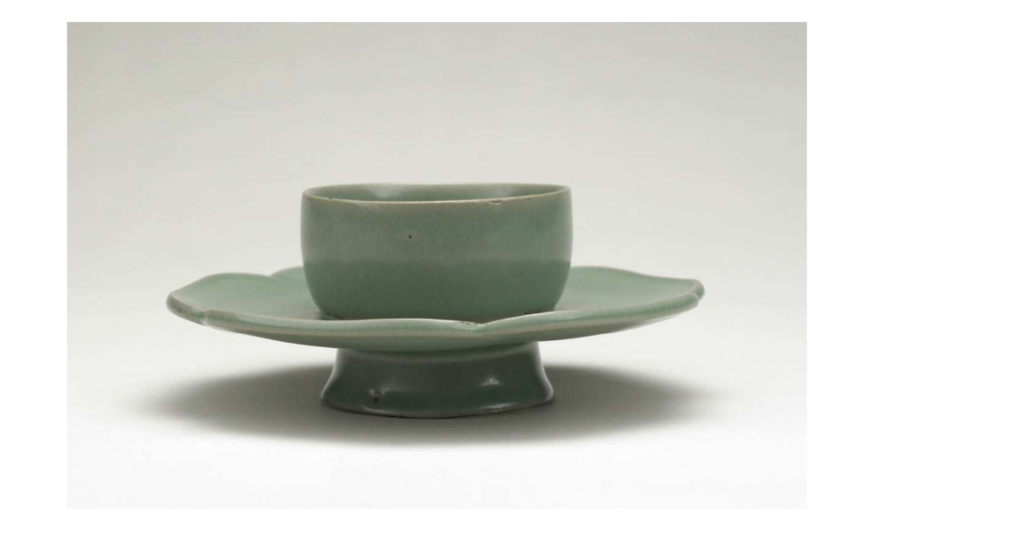
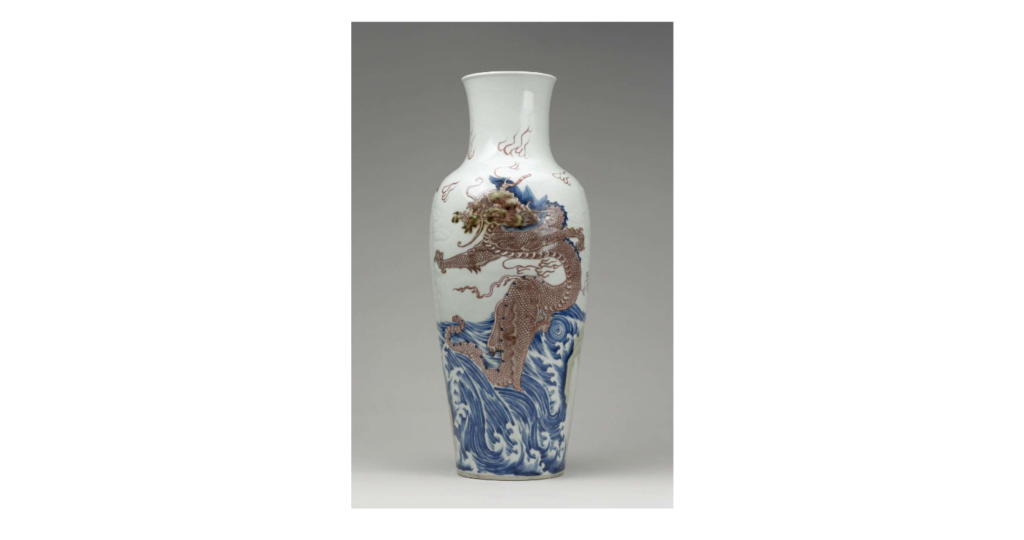
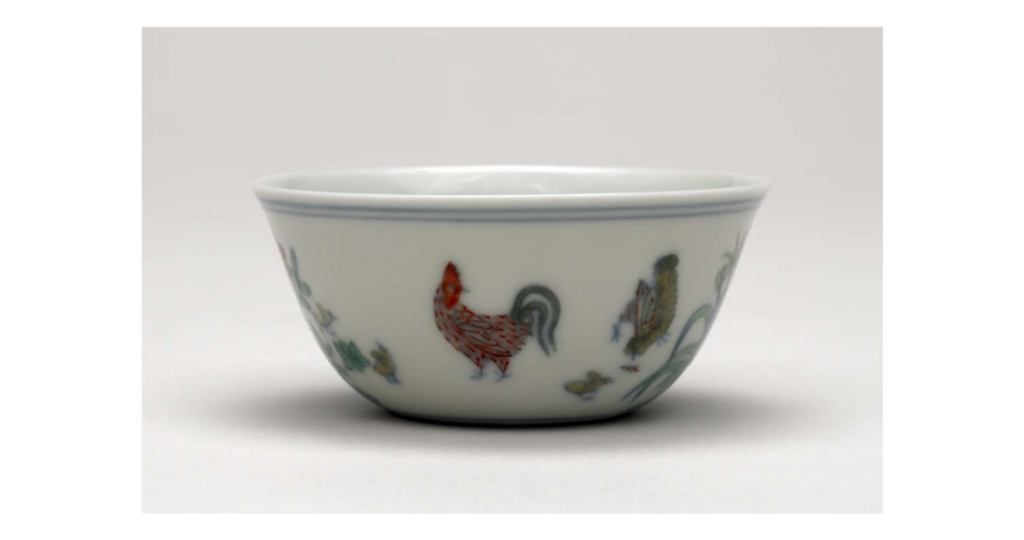
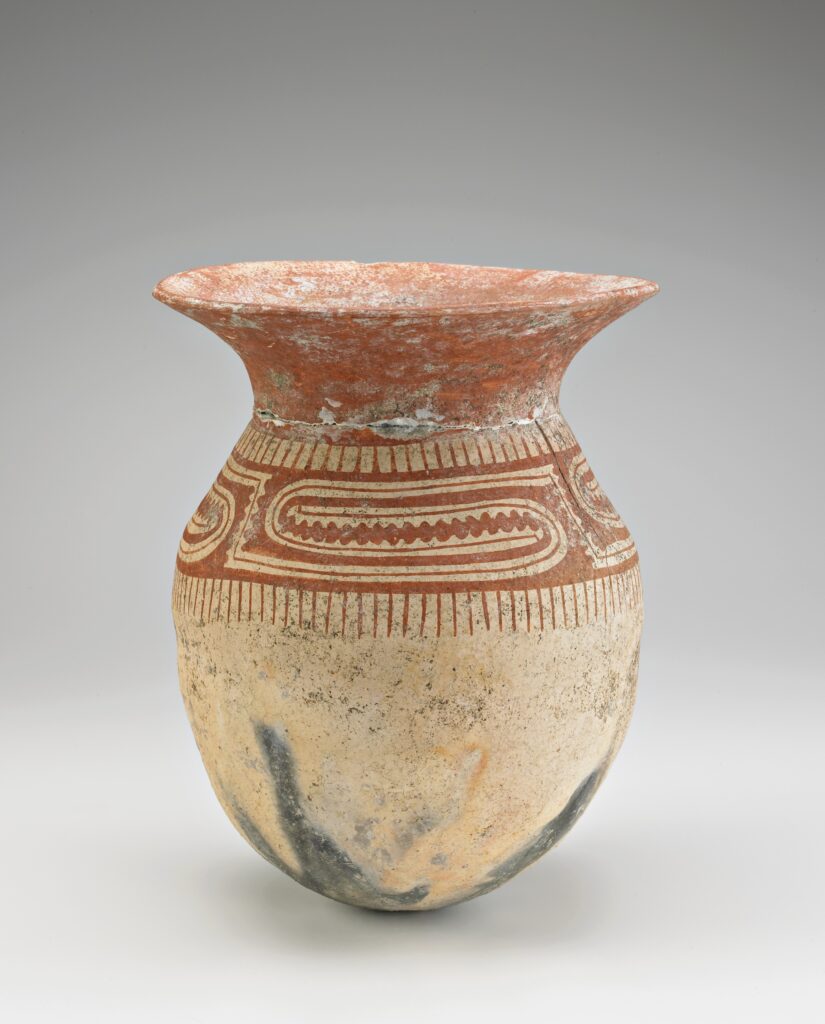
Here’s a breakdown of the ceramic production process into distinct steps:
Step 1: Raw Material Preparation
The first step in ceramic production is gathering and preparing raw materials, mainly clay, silica, feldspar, and other minerals. The clay is cleaned and mixed to achieve a consistent texture and composition, ensuring it’s free from impurities.
Step 2: Shaping the Clay
Once prepared, the clay is molded into the desired shape. This can be done using various techniques such as hand-building, wheel throwing, or slip casting. This stage requires precision and expertise to achieve the final shape before firing.
Step 3: Drying
After shaping, the ceramic piece needs to dry to remove excess moisture. This step is crucial to prevent cracking during the firing process. Depending on the thickness and size of the item, the drying period can range from hours to several days.
Step 4: Decorating Patterns
Similar to the ceramic shaping step, decorating patterns for shaped ceramic products is also done using many different methods.
Step 5: Glazing
Once cooled from the bisque firing, the ceramic is coated with a layer of glaze. This liquid mixture provides the final piece with color, a glossy finish, and a waterproof surface. Glazing can be applied using brushing, dipping, or spraying techniques.
Step 6: Final Firing (Glaze Firing)
The glazed piece undergoes a firing step, typically at temperatures between 1200°C and 1400°C (2192°F and 2552°F). This stage melts the glaze and bonds it to the ceramic body, creating a durable and visually appealing finish.
Step 7: Quality Inspection and Finishing
After the final firing, the piece is inspected for quality. This includes checking for cracks, color consistency, and surface smoothness. Any minor imperfections may be corrected through additional processes, such as polishing or touch-ups, before the product is ready for distribution.
This step-by-step breakdown provides an overview of the meticulous process involved in ceramic production, showcasing both the art and science behind each product. The ceramic manufacturing process can vary in different cultures and according to different needs and glazes.
Common Types of Ceramic Products
Household Ceramics: This category includes plates, bowls, cups, and cookware. These items are valued for their durability, heat resistance, and aesthetic appeal, making them a staple in kitchens and dining settings around the world.
Construction Ceramics:
Used for functional and decorative purposes in buildings, this type encompasses floor tiles, wall tiles, and various decorative materials. These ceramics are designed for strength and long-lasting wear, adding both utility and style to architectural spaces.
Technical Ceramics:
These advanced ceramics are engineered for use in medical and industrial applications. Examples include bone implants that aid in surgical procedures and heat-resistant ceramic plates used in high-temperature industrial processes. Their unique properties, such as biocompatibility and thermal resistance, make them indispensable in specialized fields.
Technology and New Innovations in Ceramic manufacturing
In recent years, ceramic manufacturing has witnessed significant advancements in technology and innovation, leading to more efficient processes, improved materials, and stunning aesthetic results. Here are some of the key developments in the field:
Advanced Firing Technology for Energy Efficiency:
Innovations in kiln technology have introduced energy-saving firing methods that not only reduce environmental impact but also lower production costs. These advancements allow for precise control of temperatures and firing times, which optimizes the durability and consistency of ceramic products.
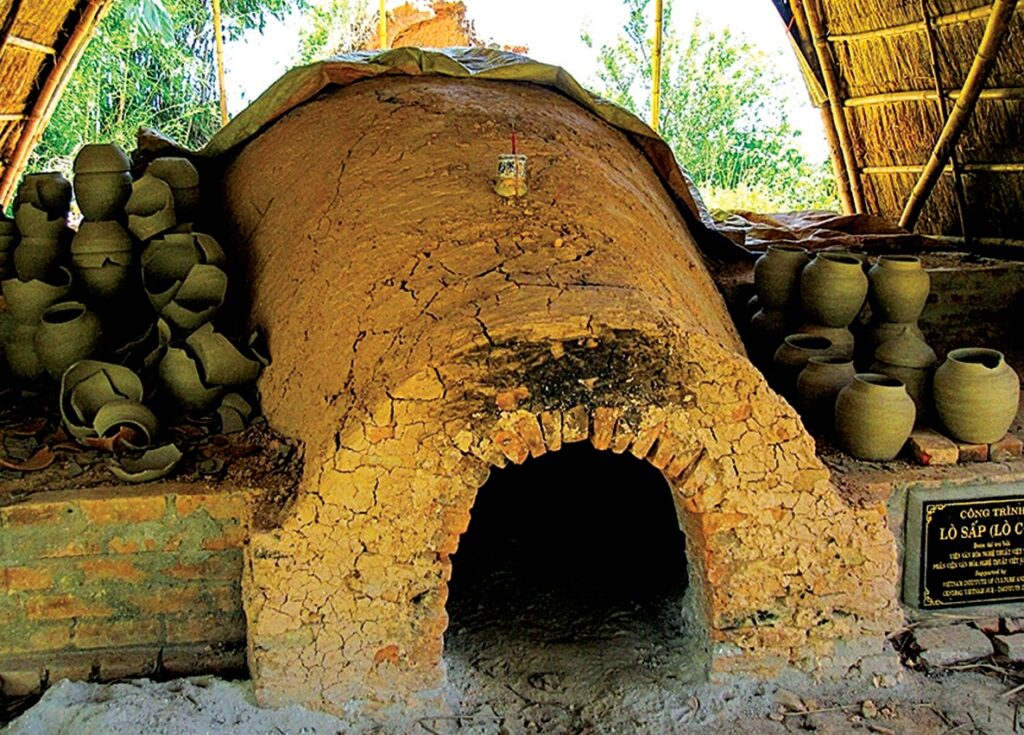
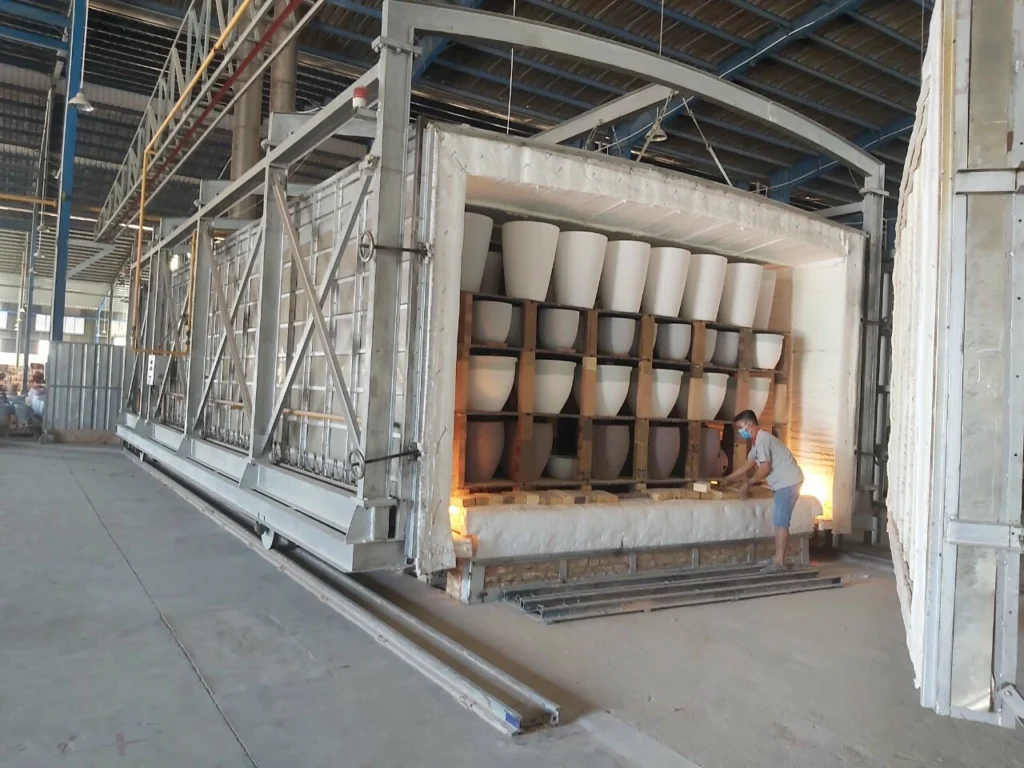
New Materials for Lighter, More Durable Ceramics:
The development of new ceramic materials has transformed the industry by enabling the production of ceramics that are both lighter and stronger. These materials not only reduce manufacturing costs but also enhance product versatility, making ceramics more suitable for a wider range of applications, from kitchenware to industrial components.
3D Printing Applications in Ceramic Manufacturing:
3D printing technology has opened up new possibilities in ceramic design and production. By enabling complex shapes and intricate detailing, 3D printing allows manufacturers to create unique, custom designs with a high degree of accuracy. This technology is also highly flexible, allowing for rapid prototyping and small-batch production, which is ideal for artists and designers.
New Glazing Techniques for Unique Color Effects:
Innovative glazing techniques have introduced a variety of new color effects, adding depth and vibrancy to ceramic surfaces. Techniques such as reactive glazes and multi-layered glazes create unique visual effects that change based on firing conditions, offering consumers a wide range of choices for decorative and functional ceramics.
These technological advances are propelling the ceramic manufacturing industry forward, making it more sustainable, efficient, and creatively diverse. As a result, ceramic products are becoming more appealing to consumers and finding new applications across multiple industries.
Development Trends and Prospects of the Ceramic Industry
The ceramic industry is experiencing steady growth, driven by rising market demand, sustainability efforts, and the potential for high-end applications:
Growing Market Demand:
Ceramic products, from tableware to tiles, are increasingly popular for their beauty and functionality. The demand for unique, artisanal ceramics is also rising, fueled by consumer interest in personalized and high-quality items.
Sustainability in Production:
Environmental awareness is pushing manufacturers toward sustainable practices, such as reducing energy use and minimizing waste. Consumers are also favoring eco-friendly ceramics, leading to innovations in recyclable and biodegradable products.
Opportunities for High-End and High-Tech Ceramics:
There is strong potential in premium ceramic products for luxury markets, as well as advanced ceramics used in high-tech industries like electronics and aerospace. High-performance ceramics with specialized properties are becoming essential in these cutting-edge fields.
Conclusion
Ceramic manufacturing continues to be a dynamic industry, balancing its rich historical roots with cutting-edge technological innovations. This evolution has allowed ceramics to remain a valuable material across multiple sectors, from household goods to high-tech applications. As consumer demand grows for both functional and aesthetically pleasing ceramics, manufacturers are increasingly focused on creating sustainable products, using energy-efficient methods, and exploring new materials that make ceramics lighter, stronger, and more versatile. Advanced techniques, such as 3D printing and innovative glazing, also enable a broader range of design possibilities, appealing to diverse markets from artisanal to industrial. The industry’s commitment to sustainability and high-end applications reflects its adaptability and resilience. Moving forward, ceramic manufacturing will likely continue to bridge the traditional and modern, proving itself essential not only for everyday use but also in emerging fields that require precision and durability. This makes ceramic manufacturing a cornerstone of both cultural heritage and forward-looking innovation, shaping the future with a material as timeless as it is transformative.
Must-Have Ceramic Pieces for Every Space
Enhance your home with our carefully selected ceramic collection. Discover timeless designs and quality craftsmanship through our affiliate links—find the perfect pieces to elevate any room!
Related Search Terms: Ceramic Manufacturing, Sustainable Ceramic Cups, Eco-Friendly Drinkware, Handmade Ceramic Products, Durable Ceramic Materials
See More